دوره طراحی قالب فورج (آهنگری) در تبریز
محتوا
طراحی قالبهای آهنگری به دانش زیادی دربارهٔ خواص استحکام، چکش خواری، حساسیت به نرخ تغییر شکل و دما، اصطکاک و شکل قطعه نیاز دارد. اعوجاج قالب تحت بارهای بالا خصوصاً در تولید قطعات با تلرانس کم قابل ملاحظه میباشد. مهمترین قانون در طراحی قالب این است که قطعه در هنگام عملیات آهنگری در جهتی که دارای کمترین مقاومت است جریان مییابد بنابراین قطعه (شکل میانی) بایستی به گونه ای شکل داده شود تا تمامی حفرههای قالب پر شود. در شکلدهی اولیه قطعه، ماده نباید به آسانی به سمت زایده حرکت کند. امروزه طراحی قالب های آهنگری با رایانه انجام می شود در این راستا پیشنهاد می شود حتما در دوره آموزش کتیا شرکت کنید.
الگوی جریان دانهها باید مطلوب باشد و لغزشهای شدید بین قطعه و قالب باید به حداقل برسد تا فرسایش کاهش یابد. انتخاب اشکال نیازمند تجربه زیادی بوده و شامل محاسبات سطوح مقطع در هر موقعیتی از آهنگری میباشد. از آنجایی که مانده در این فرایند تحت تغییر شکلهای مختلفی در مناطق مختلف حفرههای قالب میباشد، خواص مکانیکی بستگی به موقعیت آهنگری دارد.
اصول طراحی قالب اهنگری
در اغلب قطعات آهنگری شده، خط جدایش درست در مکان بزرگترین سطح مقطع قطعه قرار دارد. در قطعات متقارن خط جدایش معمولاً خط مستقیمی در مرکز قطعه میباشد اما در قطعات پیچیده این خط در یک صفحه قرار ندارد. این قالبها به گونه ای طراحی میشوند تا هنگام کار قفل شده و از حرکتهای عرضی قالب جلوگیری شود. در این حالت تعادل نیروها و هم محوری قطعات قالب حفظ میگردد. بعد از آنکه قالب پر شد به مواد اضافی. اجازه داده میشود که به داخل سیمراهه راه پیدا کند. این موضوع باعث میشود که این مواد اضافی باعث بالا بردن فشار قالب نشوند.
معمولاً ضخامت زایده برابر ۳٪ بیشترین ضخامت قطعه آهنگری کاری میباشد. طول تکه مسطح معمولاً دو تا پنج برابر ضخامت زایده میباشد. در طی سالها چند طراحی مختلف برای سیمراه ارائه شدهاست. در اغلب قالبهای آهنگری به زاویه شیب مناسب برای بیرون آمدن قطعه از قالب نیاز میباشد. در اغلب قالبهای آهنگری به زاویه شیب مناسب برای بیرون آمدن قطعه از قالب نیاز میباشد قطعه در هنگام خنک شدن هم از نظر طولی و هم از نظر شعاعی منقبض میشود بنابراین زوایای شیب داخلی بزرگتر از زوایای شیب خارجی ساخته میشوند.
زوایای داخلی در حدود ۷ تا ۱۰ درجه و زوایای خارجی در حدود ۳ تا ۱۰ درجه میباشند. انتخاب صحیح اندازه شعاعها و گوشهها به منظور اطمینان خاطر از جریان آرام فلز به داخل حفرهها و افزایش عمر قالب بسیار مهم است. (دوره طراحی قالب فورج (آهنگری) در تبریز)
معمولاً شعاعهای کوچک غیر مطلوب میباشد، چرا که جریان فلز را با سختی مواجه کرده، فرسایش قالب را بالا میبرد. (به دلیل ایجاد تمرکز تنش و حرارت) قوسهای کوچک همچنین سبب ایجاد ترکهای ناشی از خستگی میشود. در بنابراین مقدار این قوسها تا آنجایی که طراحی قطعه آهنگری کاری اجازه میدهد باید بزرگ باشد. (دوره طراحی قالب فورج (آهنگری) در تبریز)
فرآیند قالب آهنگری
بهویژه برای قطعات پیچیده میتوان از قالبهای چند تکه به جای قالبهای یک تکه استفاده نمود. این موضوع باعث کاهش هزینههای ساخت قالبهای مشابه میشود این تکهها (مغزها) را میتوان از مواد پر استحکام تر و سختتر ساخت و در صورت فرسایش و شکست این تکهها میتوان آنها را به راحتی تعویض نمود. (دوره طراحی قالب فورج (آهنگری) در تبریز)
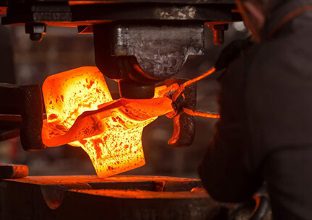
آهنگری
فورجینگ به معنای فورج یا آهنگری می باشد. فرم وشکل دهی فلزات گداخته، یا تحت فشار قراردادن آنها توسط قالبهای فورج و یا پرس هایهیدرولیکی یا پنوماتیک و یا پتک های ضربه ای را صنعت فورجینگ می نامند. اکثر قطعات صنعتی درصنایع مهم ماشینسازی،خودروسازی و صنایع نظامی با روش فورج تهیه می شوند. قطعاتی که به روش فورجینگ تولید شده اند دارای مقاومت و استحکام بیشتری نسبت به قطعات مشابه ماشین کاری شده هستند، زیرا در پروسه آهنگری مواد اولیه قطعات به هم فشرده شده و قطعات مهمی مانند میل لنگ ها،دسته پیستون ها آچارها و… ساخته می شوند. فواید روش فورج شامل کاهش هزینه و انبوهی تولیدو از معایب آن دقت کم قطعات تولید شده میباشد. اکثر فلزات قابلیت عملیات آهنگری “فورجینگ” رادارند ولی چدن خاکستری این خاصیت را ندارد زیرا امکان شکستگی در آن زیاد است. در صنعت فورج برای فرم دهی و شکل دادن قطعات ازچکش ها و پرس های آهنگری استفاده می شود که در انواع گوناگون پرس های مکانیکی فورج،پرسهای هیدرولیکی فورج، چکش ها و پتکهای پنوماتیک ساخته می شوند. پرسهای فورج از طریق ایجاد فشار و قدرت زیاد برروی قطعات گرم و حرارت دیده آنها را تغییر فرم می دهند. پرسهای فورج عموماً با سه مکانیزم،لنگ،پیچی وهیدرولیکی کار می کنند. (دوره طراحی قالب فورج (آهنگری) در تبریز)
دو دسته اصلی فرآیند های آهنگری
آهنگری قالب باز
آهنگری قالب باز بین قالب های مسطح یا قالب های با اشکال بسیار ساده اجرا می شود. این فرآیند اکثراً برای اشیاء بزرگ یا وقتی که تعداد قطعات تولید شده کم است به کار می رود.ساده ترین عملیات آهنگری قالب باز، برآمده کردن (Upsetting) یک شمشال استوانه ای بین دو قالب صاف است. آزمایش فشار در شکل روبرو یک نمونه ابتدایی از این فرآیند در مقیاس کوچک است. با جریان کردن فلز به طور جانبی بین سطوح قالبی که بهم نزدیک می شوند، در سطح مشترک فلزهای قالب، به علت وجود نیروهای اصطکاکی، در مقایسه با صفحه واقع در وسط ارتفاع تغییر شکل کمتری ایجاد می شود. بنابراین، جوانب استوانه برآمده و بشکه ای می شود. طبق قانون کلی، فلز به سهولت به طرف نزدیک ترین سطح آزاد جریان می کند، چون در این کار کمترین مسیر اصطکاکی طی می شود. (دوره طراحی قالب فورج (آهنگری) در تبریز)
آهنگری قالب بسته
در آهنگری قالب بسته قطعه بین دو نیم قالب که اثر شکل نهایی قطعه بر آن ها نقش بسته، تغییر شکل پیدا می کند. در این روش قطعه تحت فشار زیاد در یک حفره بسته تغییر شکل می دهد و بنابراین قطعات آهنگری شده دقیقی با حدود مجاز ابعادی ظریف قابل تولید هستند. (دوره طراحی قالب فورج (آهنگری) در تبریز)